Bga Solder Joint Crack Error Message
Posted : admin On 23.08.2019By re-melting the solder balls in a BGA any imperfect joints will be fixed when. 6) To convert this into 'Xbox error code' just take those numbers, but change any.
What is Causing Intermittent BGA Failures?Electronics Assembly Knowledge, Vision & WisdomWhat is Causing Intermittent BGA Failures?We're having problems with BGA devices after SMT assembly. During testing, the BGA devices are failing, if we press lightly on top of the BGA device during testing, the board passes. The Assembly Brothers, Jim Hall and Phil Zarrow, offer their advice.Board TalkWith over 35 years experience in PCB assembly, Phil is one of the leading experts in SMT process failure analysis. He has vast experience in SMT equipment, materials and processes.A Lean Six-Sigma Master Blackbelt, Jim has a wealth of knowledge in soldering, thermal technology, equipment and process basics. He is a pioneer in the science of reflow.
Bga Solder Joint Crack Error Message Version
EMS Qualification, Evaluation and Selection. SMT Process Consulting and Troubleshooting. SMT Process Development and Set-up.
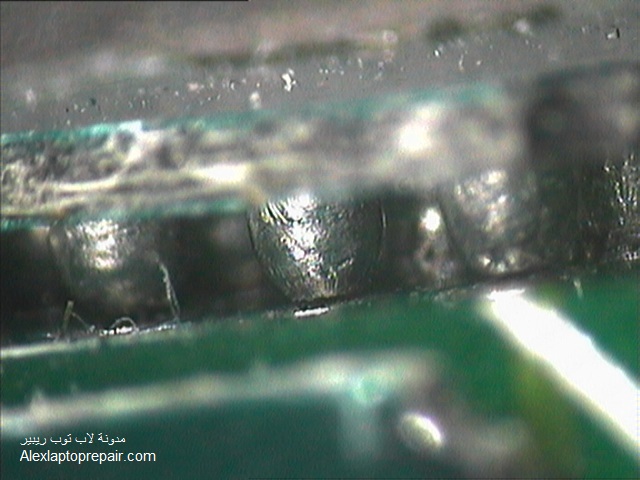
SMT Process Audits. Lead-free Process Readiness Audits.
SMT Process Optimization. On-Site WorkshopsSubmit A CommentComments are reviewed prior to posting. You must include your full name to have your comments posted. We will not post your email address.Your NameYour CompanyYour E-mailYour CountryYour Comment. TranscriptPhilWelcome to Board Talk. This is Phil Zarrow and Jim Hall of ITM fame, but also we're here for Board Talk.
I believe today we have a solder defect question, Jim, and BGA related.JimThis comes from M.S. 'We're having problems with some BGA devices after SMT assembly. During testing, the BGA devices are failing. However, if we press lightly on top of the problem BGA device during testing, the board passes.' 'What is the likely cause? Is it likely to be a solder joint failure, or something internal within the BGA package?'
PhilYeah, I hate those flexible over-molded BGA's. Well, I hate to tell you, but it's your process my boy. And there's a number of different causes.The first one that comes to my mind is inadequate solder paste height. So the question I have to ask you, 'Are you measuring your solder paste height?' If you are indeed measuring it, are you holding it to intelligent levels? Because that's another mistake we've seen often where people have very wide divergence on the low side.So, you definitely want to make sure you've got realistic levels and you're controlling it and you're not just recording it.
You're actually looking at the data, because that's going to tell you a lot right there. So, that's the first thing that comes to mind.JimOne might tend to think about a head in pillow, but I would suspect not since you're getting an open circuit on initial test. Typically with a head in pillow, there's enough contact. Although they're not soldered together, they is usually enough physical contact after the board has cooled down to give you continuity and passing tests.That's one of the biggest problems with head in pillow, they seem to pass tests, but then they become intermittent later on.
But I do suspect inadequate solder volume coupled with perhaps some amount of warpage of the package.Look at your heating profile and your cooling profiles and your BGA packages. Greg Stearns, EmersonBall co-planarity has been found to be a significant player in the formation of HIP defects, whether you use paste or tacky flux this can bite you.
If you are using a 5 mil stencil and your BGA has 8 mil co-planarity, at some point you are going to get balls that never touch the paste, so the flux never touches the ball, and warping can make it worse. Same goes for tacky flux only.
Bga Solder Balls
If the flux has been 'used' up by the time the part collapses, you may not have HIP, but you will not have the formation of a good inter-metallic.So you need to check the co-planarity spec of the BGA when you do your stencil design, you may have to Step up the BGA area. Dario Cordova, Leader Technology SolutionsCheck the lot code of the BGAs and see if the problem follows that lot code. If this is a flip-chip BGA it sounds like the under-fill underneath the die has delaminated. You can send fresh parts from that lot code out for CSAM which will detect delamination if problem is supplier issue. Also if cause by process, the delamination can be caused buy the soldering process being too hot on the component body, and/or soldering parts that have absorbed moisture.This is more pronounced concern on larger BGAs. Be sure your parts are baked and you don't exceed package (not solder) temps.
Rick Smith, HPIn addition to the soldering quality of the solder ball for the BGA, there is another issue: delamination of solder ball, why? We received customer complaints about intermittent communication coming from BGA. We performed X-Ray analysis, but no issue related to soldering was observed. We performed a destructive test by micro section of the impacted Pins of the BGA and we found cracks generated by mechanical stress.
Finally we found the real root causes and in order to confirm we performed a strain gauge measurement in different step of the process and also at the customer level. We found more than 450µm the limit of BGA delamination.
Carl Zweben, Ph. D., Zweben Consulting, USAThis is very interesting.
I am having a similar issue with units failing in the field after a variable time period (so far up to about 9 months). I've x-rayed (basic, and CT) the boards, down to the net in question, and can't find anything definitive from this.So, what would be the next step in the diagnosis of this issue. At the moment, of a batch of about 225 units, 4 have failed with an intermittent connection under the same BGA device, although on different nets.I am very keen to know what to do next. Ed Wood, EW Consult, UKWe do not totally agree with the comment about solder volume being a 'common' cause of intermittent BGA's.
As Richard has pointed out, solder paste is NOT necessary to create a reliable BGA connection. Aside from reworking BGA's, it is completely common practice to place PoP components with a flux dip and no solder paste on the top component. As long as some paste (or flux) makes it to the pads, the ball should solder.Furthermore diagnosing the root cause of an intermittent BGA can be extremely expensive, tricky, and time consuming business. There are a myriad of test that can be performed. Jose Tamayo, Jose Tamayo Co., USAOne of the most common problems that we see is related to the use of lead free solder. If you are not using vapor phase or nitrogen reflow. When the lead free solder ball becomes liquid during the reflow process, air will come in contact with the connection between the solder ball and the BGA component.
The pad on the BGA actually oxidizes because there is no flux protecting the solder joint. There is only enough flux in the solder paste to protect the bond from the PCB pad to the solder ball. If you remove the BGA, you will note that there are BGA pads that are a flat dull grey.
Solder will not wet to them. This is what is causing a bad connection.
Dennis O'Donnell, Precision PCB Services, Inc., USAWe are fabricating boards with Fine Grid BGAs. We have as in the past called out ENIG. However, there is a catch 22.This board is part of an experimental instrument for the International Space Station. We do not have the traditional NASA requirements. However, our QA wishing to follow the current NASA workmanship standards.QA is requiring that per IPC J-STD-001ES and IPC J-STD-001E all gold must be removed from the board surface with a double tinning process.This of course defeats the whole purpose of using ENIG to make the BGA surface flat.Am I missing something here? I would be very grateful for your insight on this.
Robert Meyn, Senior Systems TechnologiesIntermittent opens can be due to five (5) most common causes:1. Open internal via in main PWB. This is usually caused by initial reflow or rework without pre-baking the PWB to remove moisture. The high moisture content can lead to z-axis expansion of the PWB during reflow or rework (not always manifest as delamination), shearing the internal traces from the via barrel. This is especially true in the area of most BGA designs, with many vias.
Pushing down on the BGA can cause a intermittent re-connect.2. Same as number one above, except for the BGA substrate, which (usually) also has many vias.3.
Head-in-pillow, as was mentioned. However, solder paste is NOT NECESSARY for BGA soldering. Many experienced houses are seeing better yields by simply leaving the paste off of the pads and solder the BGA directly to the pads using the BGA solder balls only. Eliminating the paste gets rid of bridging due to misprints, head-in-pillow defects, and many other defects associated with the paste. It is NOT NEEDED in 95% percent of instances where BGAs are soldered, and is certainly not needed for rework. Just leave the apertures off of the stencil, and use a very small amount of a good tacky flux instead.4.
Pad cratering, leading to intermittent opens between the pads on the PWB and their traces.5. Many BGAs are made with temperature sensing circuits that switch off the BGA if the temperature increases above a certain limit. If it is operating at around 100 deg. F, and you press your thumb on it, this can sometimes be enough to kick it off.
January 11, 2018Intermittent BGA Test ProblemsWe're having problems with some BGA devices after SMT assembly.During testing the BGA devices are failing, however if we press lightly on the top of the problem BGA device during testing, the board passes.What is likely to be the cause? Is it more likely to be solder joint failure, or something internal within the BGA package?M. S.Expert Panel ResponsesThis sounds like a typical 'head-in-pillow' (or 'ball-in-socket') defect that is a common issue with BGAs. In this case, the joint is not really metallurgically formed, but the two metal surfaces (the solder and the BGA ball) are mechanically touching each other.The amount of contact between the ball and the solder can vary with the temperature, or with pressure put onto the part (as you indicated in your question).
This is almost certainly not an internal issue with the component itself; it is a soldering defect at the interface between the ball and the solder.There have been a lot of studies conducted and technical papers written on prevention of head-in-pillow defects. One common cause is the component or board warping just enough that the ball loses contact with the solder paste just before the paste begins to reflow.Another cause is that the reflow profile drives a Delta T across the component that can create some 'tilting' of the component, again just enough to let the ball lose contact with the paste just as the board reaches the liquidus temperature.This is often a complicated defect resolution, so I would suggest carefully studying the defect location(s) - are the defects always occurring on the same parts, same locations on the same parts? Is it directional - if you turn the board 180 degrees heading into the oven, does the amount of locations of the defects change?I would also suggest to contact your solder paste supplier to see if they have any tips to help with this. If you contact me directly, I can provide a few papers to help get the process started for you.General Manager - Electronic Assembly Americas.
Smith has been supporting customers in the electronics assembly industry since 1994. His expertise is focused on solder paste printing and reducing soldering defects.
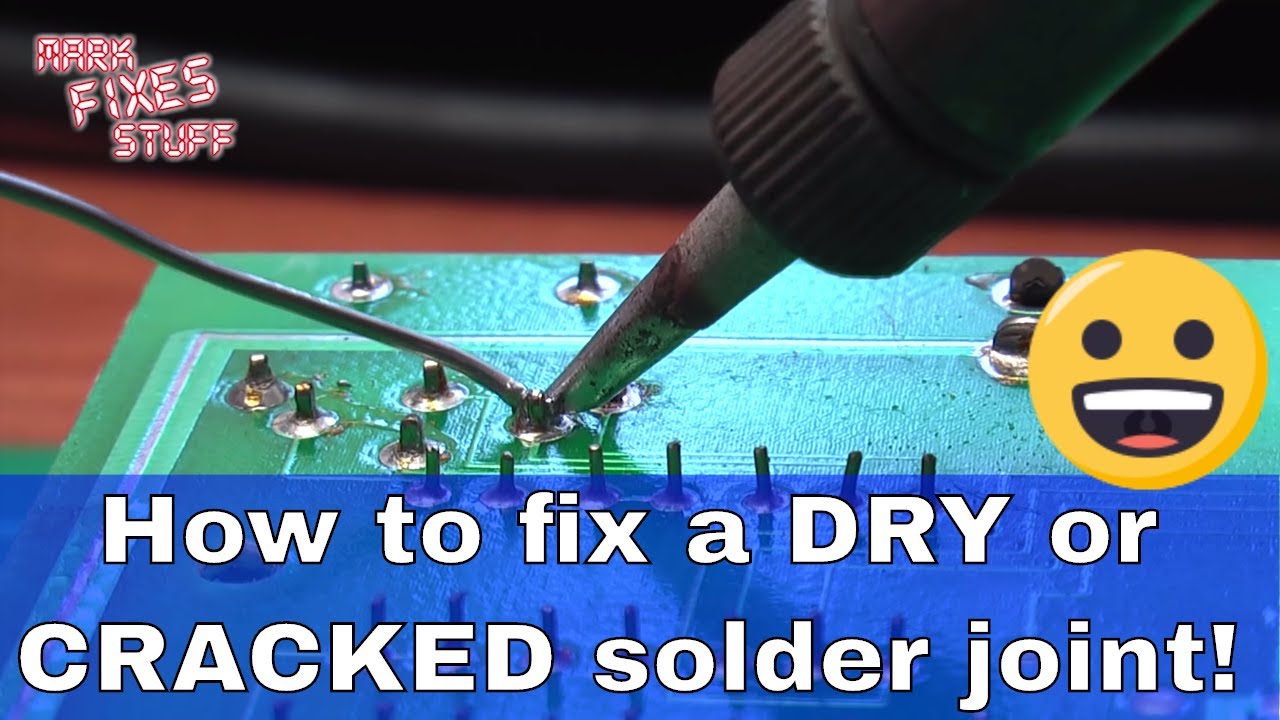
He holds a BS in Chemical Engineering and an MBA in Marketing. He has authored several papers in trade magazines and at industry conferences.
He is an SMTA Certified Process Engineer.You are most likely seeing solder balls underneath the device that did not reflow properly and therefore are not making electrical connection to their associated pad(s), although there could be other reasons causing electrical connection failure.However, in my experience as a contract manufacturer who is exposed to all types of designs this one is the most probable. Applying pressure on the top of the device during operation is causing the improperly reflowed solder balls to forcibly make electrical connection.
David has been active in all areas of the contract electronics manufacturing industry for over fifteen years. He is currently in charge of all Sales and Marketing related activities for Technical Manufacturing Corporation.This would seem to be a classic example of what is known as head in pillow failure.The effect is traditionally caused by the volume of solder paste, and therefore the flux being too low.During the reflow process due to the low volume of flux, the activity or fluxing action is used up before the solder powder reaches melting temperature.
This reduces the ability of the solder to break the surface tension or wet to the surface of the BGA ball and causes a reflowed solder pad in contact, but not soldered to the BGA ball. It will create a contact joint, but not a soldered joint. The upshot of this is that there is initially some conductance or only conductance if pressure is applied. On the long term this contact will deteriorate due to oxidation.The best way to improve this effect is to ensure a better or more consistent volume of solder paste that is printed to reduce the risk of insufficient volume or look at improving the reflow profile to reduce the stress or risk of drying out the flux before reflow.The other potential cause is PCB warpage of the BGA during reflow.
If the BGA warps up, there is a risk that both, ball and solder, reflow as normal, but they are not in contact due to warpage. As the solder solidifies during cooling down of the reflow profile, they then come into or near to contact.This means that during test when pressure is applied you achieve contact and get a pass, but in realty there is a gap and no contact is made.
Again modifying or checking the reflow temperatures can help reduce this risk.A simple cross section or in some cases an x-ray may help to show to the root cause.Marketing. Douglass Dixon is the Chief Marketing Officer for 360 BC Group, a marketing agency with offices throughout the US. 360 BC specializes in consulting and implementing successful marketing programs that utilize the latest in marketing, sales and technology strategies. As an electronics veteran, Dixon has worked in the industry for over 30 years for companies like Henkel, Universal Instruments, Camelot Systems, and Raytheon.
Dixon's electronics industry experience includes a broad skill set that includes engineering, field service, applications, product management and marketing communications expertise.This sounds to me like a textbook case of Head-in-Pillow (HiP) defects. What happens in this case is that during reflow, the BGA warps, causing some of the balls to lift out of the paste.
The paste and ball then melt separately.During cool-down the BGA relaxes and the ball then rests on the reflowed paste, but because of oxide buildup on the surfaces of both the ball and the paste, combined with a flux that no longer is active enough to clean the surfaces, the ball and paste do not coalesce together. This causes the joint to be conductive when in contact, but a slight shift can cause failure of the joint.It seems that if you are able to press down on the BGA and cause it to work again, HiP is your cause. It's hard to diagnose this for sure without tearing off a BGA or two and looking to see if the joints on the corners are well formed, because in a top-down x-ray the joint will look normal.For more information by a colleague of mine.Product Support Specialist. Brook is Product Support Specialist for PCB Assembly Materials at Indium Corp. With a background in Chemical Engineering and previous experience with conductive adhesive new product development, she provides expertise in choosing the right materials and processes to optimize PCB assembly operations.Most likely cause is a Head on Pillow (HoP) joint failure under the BGA, where the solder paste and the BGA solder ball are not merged, or in contact, following reflow. Downward pressure on the BGA makes an electrical contact on the joint, which releases as the finger pressure is removed and the failure re-establishes.An x-ray view at an oblique angle should confirm this non-destructively as the ball and the paste will appear as distinct separate entities compared with a single entity that would be a correctly re-flowed ball. An example image is attached - note the variation in the ball shapes - indicating an uneven response to the reflow and the Head on Pillow joints having the separate 'shadow' like structure with respect to the solder ball.If x-ray inspection shows that all of the BGA joints are consistent then this failure is not due to Head on Pillow joints and it could be caused by warpage of the device cracking and lifting the device away from the board.
Alternatively, it could be through a failure within the BGA package itself where an internal joint has failed and pressure applied, again, re-makes the joint.Product Manager. Bernard has been the X-ray Systems Product Manager at Dage for over 5 years and have been involved in all aspects of x-ray inspection and test for printed circuit board assembly applications. Prior to this, Dr. Bernard was working with radiation measurement instrumentation.I expect the most likely cause to be open solder joints below the BGA device.
Pressing down on top of the package provides temporary contact.The likely root cause is warpage of the BGA or the board during reflow. Oftentimes, this will be resolved by extending preheat or slowing the ramp rates in your reflow profile, allowing some stress relief.A less likely cause is delamination of BGA due to moisture. Adequate pre-bake should resolve this issue.General Manager. Zamborsky serves as one of OK's technology advisers to the Product Development group.
Replying to Sam Lau, I must tell this was a highly debated issue.The diagnose from the lab that performed the metallographic cut was the defect looked very much like black pad, a known issue of ENIG finishing when phosphorous contaminates the nickel intermetallic.The BGA manufacturer said it cannot be black pad as they never use ENIG. They use electrolytic nickel immersion gold instead which does not contain phosphorous.In any case the brittle fracture happened between the NI/Sn intermetallic layer and the underlying Ni layer which points to a BGA pad finish issue.
The solder wetted and formed an intermetallic bond with the nickel but for some reason the bond between the Ni and the intermetallic layer was too weak and cracked.If the problem was due to a mechanical stress between the PCB and the BGA the fracture would be expected to be in the solder, and not at the NI/intermetallic interface.Just my two cents. Pedro Tort, DigiProces, Spain. Don't discard component defect as a cause of BGA ball bad contact. Unlikely but it happens.We had the same problem a few weeks ago. One of our customers found two defective boards from different production batches showing the same defect on the same BGA ball. When pressing down on the BGA, the circuit functionality was OK. Removing the pressure made the defect come back.
The functional test located the problem on one of the external row of balls.We suspected as well it could be a warpage or a reflow related issue, but a review of the assembly parameters for printing and reflow didn't show anything wrong.We sent one of the defective boards to an external lab to perform a metallographic cut at the suspected solder joint. The image obtained shows very clearly the solder joint was OK, but there was a sharp separation between the upper part of the ball and the component body.Maybe it is not a very common defect, but I can tell you it happens. Pedro Tort, DigiProces 6 Liberty Square #2040, Boston MA 02109 USAJeff Ferry, Publisher Ken Cavallaro, Editor/Business ManagerCopyright © Circuitnet Media LLC. All rights reserved.